Poradnik
Spis treści:
- Klasyfikacja czystości powietrza w pomieszczeniach czystych
1. Klasyfikacja czystości powietrza w pomieszczeniach czystych
Klasy czystości powietrza według US Federal Standard 209E
W gałęziach przemysłu takich jak przemysł elektroniczny, farmaceutyczny, spożywczy,
chemiczny, włókienniczy pomieszczenia klasyfikuje się najczęściej ze względu na ilość
zanieczyszczeń cząstkami stałymi występujących w powietrzu wewnętrznym. Daną klasę powietrza
określa się przez podanie maksymalnej liczby cząstek o określonej średnicy i większej w jednostce
objętości powietrza. W Polsce do 2002 roku nie było wymagań dotyczących pomieszczeń czystych,
jednak starano się utrzymać pewien standard bazując na normach i standardach zachodnioeuropejskich.
Najczęściej stosowaną normą była amerykańska norma Federal Standard 209.
Ostatnie, piąte wydanie z 11 września 2002 zostało oznaczone literą E.
Pełny tytuł tej normy brzmi: "Klasy zanieczyszczenia cząsteczkami zawieszonymi w powietrzu w czystych
pomieszczeniach i czystych strefach".
Norma ta wprowadza podział na klasy znormalizowane i dopuszcza
alternatywne klasy czystości powietrza dla czystych pomieszczeń i czystych stref w oparciu o określone
stężenia cząstek zwieszonych w powietrzu. Opisuje ona metody weryfikacji czystości powietrza i wymagania
ustanowienia planu monitorowania czystości powietrza. Podaje ona również metodę określania i opisywania
stężeń bardzo drobnych cząstek. Norma nie określa właściwości fizycznych i chemicznych cząsteczek
zawieszonych w powietrzu. Nie podaje także zależności pomiędzy stężeniem cząstek zawieszonych w powietrzu
a stężeniem mikroorganizmów unoszących się w powietrzu. Granice stężeń w poszczególnych klasach wg US Federal
Standard 209E przytoczono w tabeli nr 1.
Tabela 1. Podział na klasy czystości wg US Federal Standard 209E [1]
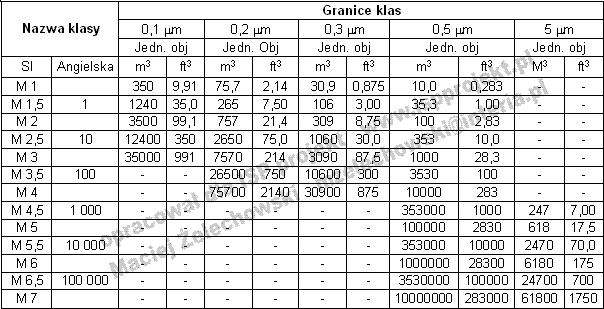
W wersji piątej tej normy wprowadzono oznaczenie według jednostek SI,
jednak jeszcze nadal jednostki angielskie są częściej używane przez inżynierów.
Gdy są specjalne warunki norma zezwala na określenie również klas pośrednich innych
niż zawarte w tabeli. Wówczas granicę stężeń można obliczyć można ze wzoru:
Liczba cząstek/m3=10M/(0.5/d)2.2 (1)
gdzie:
M - jest to liczbowe oznaczenie klasy oparte na jednostkach SI,
d - jest wymiarem cząstki w mikrometrach.
Klasy czystości według PN-EN ISO 14644-1:2002
W 2002 Polski Komitet Normalizacyjny wprowadził normy sankcjonujące standardy europejskie m.in.:
PN-EN ISO 14644-1:2002 Pomieszczenia czyste i związane z nimi środowiska kontrolowane - Część 1:
Klasyfikacja i czystość powietrza. Norma ta wprowadza 9 klas czystości powietrza.
Określa ona, jakie mogą być maksymalne stężenia poszczególnych rozmiarów cząstek z przedziału od
0,1-5,0 mm. Klasyfikacja czystości powietrza według PN-EN ISO 14644-1:2002 została przedstawiona
w tabeli nr 2.
Tabela 2. Podział na klasy czystości wg PN-EN ISO 14644-1:2002 [2]

Maksymalne stężenia dla poszczególnych cząstek w danej klasie można określić ze wzoru:
(2)
gdzie:
Cn - maksymalne stężenie cząstek zawieszonym w m3 powietrza o rozmiarach równych i większych niż D,
D - rozmiar rozpatrywanych cząstek w mikrometrach,
N - nazwa klasy czystości według ISO nie przekraczając klasy 9. Można wyznaczać klasy pośrednie z dokładnością do 0,1.
Na rysunku nr 1 pokazano graficzną formę podziału na klasy. Wykres oparty jest na obliczeniach wykonanych na podstawie wzoru (2).
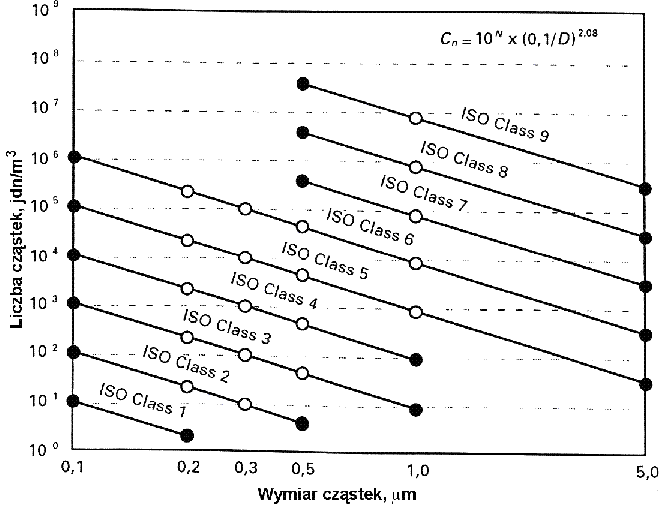
Rys. 1. Podział na klasy czystości wg PN-EN ISO 14644-1:2002 [2]
Klasy czystości według rozporządzenia MZ z dnia 3 grudnia 2002 roku
Rozporządzenie Ministra Zdrowia z dnia 3 grudnia 2002 roku zawarte w Dzienniku Ustaw z Dzienniku Ustaw
z dnia 21 grudnia 2002 roku wprowadza przepisy w sprawie wymagań Dobrej Praktyki Wytwarzania.
Rozporządzenie to określa wymagania Dobrej Praktyki Wytwarzania, których spełnienie jest warunkiem
uzyskania zezwolenia na wytwarzanie środków farmaceutycznych. Określa, jaka klasa czystości powietrza
musi być utrzymywana w pomieszczeniu lub określonej strefie przy produkcji leków.
Rozporządzenie szczegółowo omawia jak powinna przebiegać produkcja leków sterylnych i niesterylnych.
Przy produkcji tych leków powinny być zachowane szczególne wymagania, mające na celu zminimalizowanie
ryzyka zanieczyszczenia mikrobiologicznego oraz mechanicznego. Rozporządzenie reguluje szczegółowo metodę
oznaczania czystości mikrobiologicznej i zanieczyszczeń cząstkami mechanicznymi i nakazuje stosować
normy CEN/ISO. Według rozporządzenia produkcja powinna spełniać następujące wymagania:
- produkcja produktów sterylnych powinna odbywać się w pomieszczeniach czystych, do których kadra pracownicza i niezbędny sprzęt wprowadzany jest przez śluzy powietrzne. Pomieszczenia czyste powinny być utrzymane w odpowiednich standardach czystości,
- wszystkie czynności począwszy od przygotowania składników po napełnianie powinno przebiegać w oddzielnych pomieszczeniach w obrębie obszaru czystego,
- wytwarzanie produktu sterylnego dzieli się na: preparaty, które można sterylizować w opakowaniu bezpośrednim i preparaty produkowane aseptycznie,
- wytwarzanie produktów sterylnych powinno przebiegać w obszarze, w którym utrzymany jest odpowiedni poziom czystości środowiska, w celu minimalizacji możliwości zanieczyszczenia produktu.
Przy wytwarzaniu produktów sterylnych farmaceutycznych wyróżnia się cztery klasy czystości powietrza:
- klasa A - jest to klasa, w której wykonywane są czynności największego ryzyka np. napełnianie, zamykane korkami, wykonywanie aseptycznych połączeń, miejsca gdzie produkt ma kontakt ze środowiskiem,
- klasa B - klasa ta stanowi najczęściej rolę strefy oddzielającej klasę A od klasy C,
- klasa C i D - są to pomieszczenia, w których przeprowadza się mniej krytyczne etapy wytwarzania produktów sterylnych np. przygotowanie roztworów.
W tabeli nr 3 zestawiono klasy czystości powietrza wg rozporządzenia Ministra Zdrowia z dnia 3 grudnia 2002 roku.
Tabela 3. Podział na klasy czystości wg rozporządzenia Ministra Zdrowia z dnia 3 grudnia 2002 roku [3]
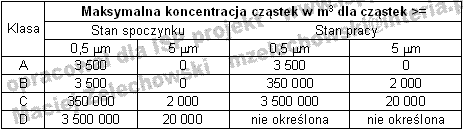
Stan spoczynku oznacza, że w pomieszczeniu pracują wszystkie urządzenia bez odslugi personelu. Stan pracy oznacza, że w pomieszczeniu pracują wszystkie urządzenia i przebywa personel. Przykładowe czynności, które mogą być wykonywane w pomieszczeniach określonej klasy, podano w tabeli nr 7.
Tabela 4. Przykładowe czynności, które mogą być wykonywane w pomieszczeniach określonej klasy [3]
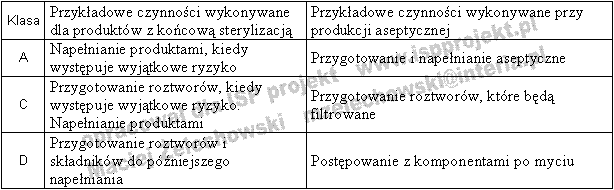
W porównaniu do U.S. Federal Standard209e i PN-EN ISO 14644-1:2002 w rozporządzeniu zostały określone dopuszczalne zalecane limity zanieczyszczeń mikrobiologicznych mogące wystąpić w pomieszczeniu czystym w stanie pracy w poszczególnych klasach. Dopuszczalne limity zanieczyszczeń mikrobiologicznych zamieszczono w tabeli nr 8.
Tabela 5. Zalecane limity zanieczyszczeń mikrobiologicznych w pomieszczeń czystych wg rozporządzenia Ministra Zdrowia z dnia 3 grudnia 2002 roku [3]
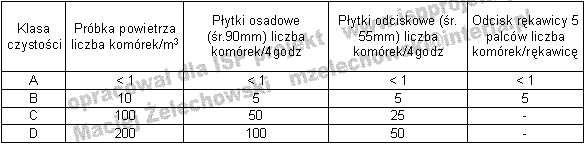
Poziom zanieczyszczenia powietrza cząstkami i zanieczyszczeniami mikrobiologicznymi przy produkcji leków sterylnych powinien być monitorowany. Monitorowanie powinno być prowadzone w sposób ciągły.
Klasy czystości w przytoczonych normach i w rozporządzeniu nie zawierają dużych rozbieżności. Można stosować nazewnictwo zamiennie z przytoczonych tu norm i zostanie ono odpowiednio zrozumiane.
Rozporządzenie określa, że wytyczne dla maksymalnej dozwolonej liczby cząstek "w spoczynku" odpowiadają wartościom obowiązującym w USA (United States Federal Standard 209 E) i normom ISO w następujący sposób:
klasy A i B odpowiadają klasie 100, M 3.5, ISO 5; klasa C odpowiada klasie 10.000, M 5.5, ISO 7 i klasa D odpowiada klasie 100.000, M 6.5, ISO 8. Jednak po dokładnym przeliczeniu widać niewielkie różnice w
ilości ziaren wg poszczególnych norm. Tabela nr 9 przedstawia zestawienie klas powietrza wg przytoczonych norm.
Nie przytoczono tutaj innych mniej znanych aczkolwiek używanych w Polskich zakładach farmaceutycznych norm zachodnich, czyli:
- VDI 2083 - norma Niemiecka,
- BS 5295 - norma Angielska,
- AFNOR 44101 i 44102 - normy Francuskie.
Jednym z warunków uzyskania klasy A jest zastosowanie przepływu laminarnego powietrza. System nawiewu laminarnego powinien zapewnić jednorodną prędkość przepływu powietrza w miejscu pracy. Prędkość przepływu laminarnego wynosi 0,45m/s z tolerancją +/-20%, co w efekcie daje przedział 0,36÷0,54 m/s.
W celu uzyskania odpowiednich klas czystości pomieszczenia, krotność wymiany powietrza powinna być uzależniona od wydzielającego się strumienia zanieczyszczeń, wielkości pomieszczenia, wyposażenia i liczby pracowników w pomieszczeniu. Układ uzdatniania powietrza dla klas A, B i C powinien być wyposażony w odpowiednie filtry, takie jak HEPA lub ULPA.
Tabela 6. Porównanie klasyfikacji pomieszczeń czystych wg rozporządzenia MZ, U.S. Federal Standard 209d,e i PN-EN ISO 14644-1:2002 [3]
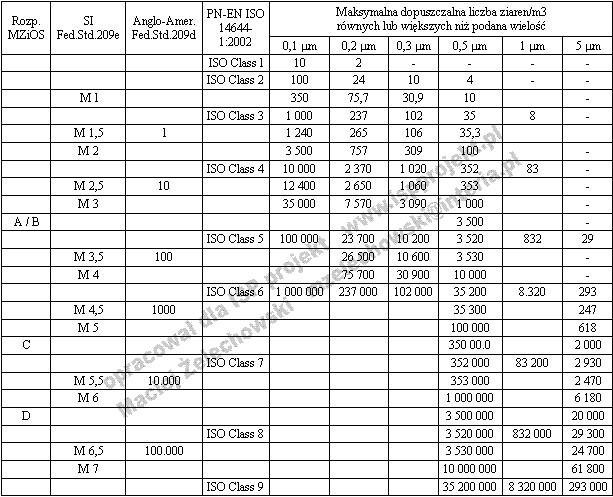
Strefy czystości powietrza
Ze względu na brak wymagań urzędowych, firmy farmaceutyczne, na podstawie monitoringu higieny prowadzonego w swoich wytwórniach, ustalały właściwe dla wytwarzania leków, wymagania dla jakości powietrza, powierzchni pomieszczeń, urządzeń, ubrań i poruszania się personelu. Powszechny był podział na trzy strefy. Podział ten stosowany jest do dziś:
- strefa czarna - jest to strefa do której zalicza się pomieszczenia nie związane bezpośrednio z produkcją: warsztaty naprawcze, zaplecze techniczne, pomieszczenia socjalne, magazyny surowców oraz tzw. szatnie brudne lub pierwszego stopnia. W nazewnictwie farmaceutycznym strefa ta nazywana jest także jako strefa niekontrolowana,
- strefa szara - jest to strefa, w której prowadzi się produkcję niesterylnych form leków. Strefa szara czasami jest dzielona na strefę szarą czystą i szarą kontrolowaną. Przeprowadzanie operacji technologicznych, w których produkt może być narażony na kontakt ze środowiskiem np. pakowanie pierwotne, wytwarzanie produktów luzem powinno przebiegać w warunkach właściwych dla strefy szarej czystej. Wymagania czystości powietrza i ubrań personelu są zbliżone do klasy D w strefie białej. W strefie szarej kontrolowanej przeprowadza się takie procesy jak pakowanie wtóre bądź transport wewnętrzny. W pomieszczeniach strefy szarej wymagany jest monitoring mikrobiologiczny. W tej strefie dopuszcza się produkcję niektórych tabletek, drażetek, maści i syropów.
- strefa biała - jest to strefa, w której przeprowadza się czynności produkcyjne związane z wytwarzaniem leków jałowych. W strefie białej wyróżnia się cztery klasy czystości powietrza A, B, C i D.
Produkcja leków sterylnych jest jednym z najtrudniejszych działań produkcji farmaceutycznej. Stworzenie warunków, które eliminują ryzyko zakażenia krzyżowego przez cząsteczki mechaniczne i pirogeny wymaga ogromnego nakładu inwestycyjnego. Produkcja sterylna dzieli się na:
- preparaty, w przypadku których sterylizacja może przebiegać w opakowaniu bezpośrednim,
- preparaty produkowane aseptycznie.
Sterylnych warunków podczas produkcji wymagają leki przeznaczone do wstrzykiwań, do oczu, do jam ciała, na otwarte rany, tabletki do implantacji, antybiotyki. Produkcja preparatów, które w końcowej fazie produkcji poddaje się sterylizacji może przebiegać w klasie C. Preparaty aseptyczne, których w końcowej fazie nie można poddawać procesowi sterylizacji należy produkować w klasie A/B. Preparaty, które będą poddane filtracji sterylizującej podczas procesu technologicznego, można sporządzać w klasie C, ale proces sterylizacji musi odbywać się w klasie A.
Bibliografia:
[1] Federal Standard, Airbone particulate cleanliness classes in cleanrooms and zones. Fed-Std-209e, 1992.
[2] ISO 14644-1 "Cleanrooms and associated controlled environments - Part 1: Classification of air clean liness"
[3] Dziennik Ustaw nr 224 artykuł 1882 z 2002 roku.
[4] Praca zbiorowa. "Poradnik GMP. Dobra praktyka wytwarzania środków farmaceutycznych i materiałów medycznych".
Projekty instalacji sanitarnych
|